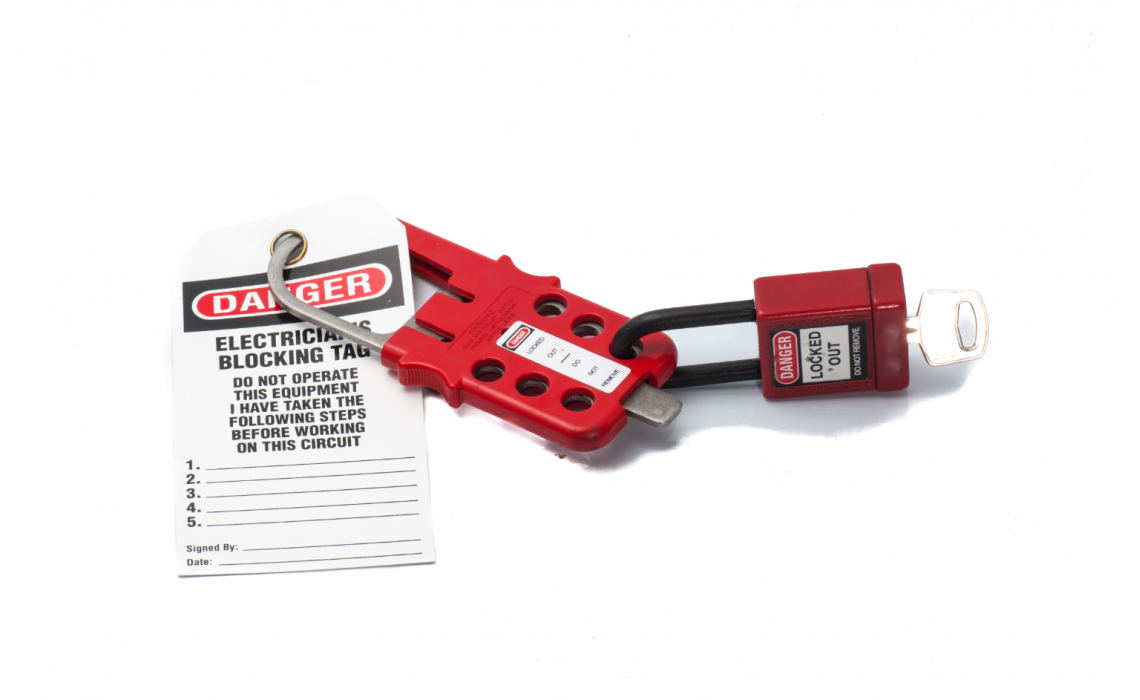
Failure to lockout and tagout leads to costly losses
FAILURE TO LOCKOUT/TAGOUT LEADS TO COSTLY LOSSES
While many might think of lockout and tagout procedures as something that's not necessary or only necessary in certain situations, we can assure you that it is necessary procedure for maintaining not only a safe workplace, but a successful business.
Failing to incorporate proper lockout procedure could lead to personal injury, it could also lead to additional problems, mainly financial, even if nobody is injured.
Receiving a fine from OSHA could be one problematic and costly effect of failure to lockout in the workplace, but some people seem to think that OSHA isn't going to show up. Or that there's no use in performing lockout/tagout because of one reason or another that someone might justify. However, consider that there are other aspects unrelated to OSHA and personal injury that could end up costing a large sum, or possibly even your business. What might it be? Insurance; and we're not talking about health insurance.
Nowadays, we know that insurance companies will often send investigators on site to inspect not only damages, but the root cause of the problem behind an insurance claim - and if something doesn't add up, don't expect to be compensated for any losses. It's common practice for insurance companies to protect their investment and best interests and to only pay out when deserved. Of course, if they find that the cause of the damage was the result of avoiding or failing to follow certain mandated safety procedures, they'll be denying the insurance claim quite easily.
For example, let's say that routine maintenance is being done on a production facility and part of that maintenance requires that certain power sources be locked out. Someone decides that they don't need to perform lockout during this maintenance, and something unexpected happens, leading to a large fire that destroys the facility or parts of the facility. If the insurance company can say that the damage was caused as a result of failing to lockout, they will not be reimbursing for the damages, which could cause a serious financial burden or even a complete loss of business.
Accidents happen, and they happen everyday. That's one of the main reasons we have insurance. But, when those accidents happen because of neglect, there is no guarantee, nor is their a obligation, for your insurance company to reimburse you financially.
While we're not trying to use fear here, we're hoping to make it clear that this is just one of the many reasons that lockout is an important factor to a safe and prosperous workplace and business. Not only does it help to ensure that workers will go home safely and without personal injury, it also helps to ensure that the business will progress forward without financial injury.
Whether you're an employee or an employer, do the right thing and follow proper procedures for lockout in your business or place of work. While it make take a few extra minutes, it can save a life; or even many lives.
LACK OF LOCKOUT LEADS TO SERIOUS INJURY
Where workplace safety is concerned, lockout and tagout play a much larger role than ne might assume.
While the decision not to perform a lockout/tagout under a given circumstance might seem minor under many circumstances, the resulting risk of injury can often be much more serious than the average workplace injury. This is generally due to the hazards presented by the type of equipment that requires lockout. For example, a properly functioning piece of large industrial equipment can easily cause injuries such as electrocution, dismemberment, severe burns and the like. Naturally, a broken or malfunctioning piece of equipment poses a greatly increased risk of injury - especially if it hasn't been properly locked and tagged out.
In many industries, worker activity determines the profit. In other words, the more product that can be manufactured or processed, the better. While workers might be expected to maintain a rapid pace in many situations, this pressure to perform can often negate proper safety procedure. From one aspect, a worker who is working to fast might be more likely to slip-up and have an accident due to the rapid pace - and from another perspective, ensuring the job is done safely and properly might mean it takes longer; something management might frown upon.
A piece of equipment that is being operated at a dangerous pace surely poses an increased risk for injury, just as a machine that isn't routinely maintained is more likely to malfunction. Under normal lockout/tagout procedure, complete systems may need to be shut down which affects the ability to produce and can often be time consuming. Sometimes locking out a specific piece of equipment can even mean that other functional equipment in the vicinity is also rendered inoperable, even if it's functioning perfectly. Many times employers and/or management are willing to take the risks in order to keep number up and likewise, employees are willing to follow the orders of management in order to keep their jobs.
Lockout/tagout applies to such a broad array of equipment and systems that there really is no easy answer or a catch-all solution to reduce injury rates. From electric boxes and systems to steam pipes, chemical systems, production line equipment, high pressure pumps and vales, and even nuclear facilities. The situations are all vastly different and that's why it is important to do the right thing - always follow the proper lockout procedure.
Not only will lockout/tagout save lives and prevent injury, it also saves money in the long run. Accidents can be costly, and one has to consider that it's not just damage to people that you should be worried about - damage to equipment can also be very costly. All standards that have been set into place by OSHA in regards to Lockout/Tagout are aimed at protecting workers, preventing disaster and safeguarding employers against liability. If a major accident occurs and something is locked out properly, it can legitimately be considered an accident. But if failure to comply with lockout procedure is the cause of the incident, it's not really an accident and could have been prevented.
Help prevent serious injury to yourself and others in the workplace by insisting on following the proper lockout procedure no matter what. You don't want to suffer the aftermath of an unfortunate injury or death due to the fact that corners were cut.
Talk with co-workers, management, employers and/or employees and devise a plan to ensure that lockout is always performed, correctly and without delay when necessary.
LOOKOUT FOR LOCKOUT - STAY SAFE BY PRACTICING LOCKOUT & TAGOUT ON THE JOB!
Depending where your place of business or employment is, you may or may not be familiar with the Lockout/Tagout process. Locking out (lockout) and tagging out (tagout) is part of a safety process that's often called lockout-tagout (lockout boxes, lockout padlocks, valve lockout...). Most commonly used in industrial settings, this is the process of disabling and securing a machine or piece of equipment prior to cleaning, maintenance or repair. The whole purpose of the lockout procedure is to ensure there is no power, no residual energy being stored and no moving parts that could cause an emergency situation such as fire, electric shock, personal injury or even death.
Locking out applies to practically any device, mechanism, machine, or piece of equipment that produces energy or uses energy to operate. This includes a vast array of industrial equipment which is far too long to list here. However, to familiarize yourself with the type of equipment that would require lockout we'll mention some of the more common ones, such as:
• Drilling Presses, Brake Presses, Saws, Lathes and other equipment designed to cut, bend or modify heavy materials.
• Mixers, Shredders, Blenders, Sorting Machines, Cleaning Tanks, Ovens, Compactors, Incinerators and other equipment that get filled with material.
• Piping systems, cabling systems, any equipment under water or steam pressure, hydraulic equipment & lines, hazardous chemical piping, electrical equipment, power systems, fuse boxes, electronic switching systems and furnaces/boilers.
• Forklifts, Front Loaders, Excavators, Steam Rollers, Cranes, and all sorts of other motor vehicles.
If a piece of machinery can pose a risk to those who might try and use it, then it needs to be effectively locked out until it's been repaired. Additionally, mechanically sound equipment should be locked out during maintenance to prevent accidental or unexpected use during maintenance.
The graphic below is a safety sheet that reminds people about the need for lockout & ragout. Click the image to reveal it in its full size to make a printable reminder to hang in the office, shop or near potentially hazardous equipment.
While there are all different types of lockout/tagout situations, there are also plenty of products to make the lockout process go smoothly - even for specialized equipment. Stay tuned to our blog and check out our past posts to learn more about the lockout & ragout process. Also, feel free to ask us about anything you'd like to see covered in our blog.
BE SAFE & BE SMART. LOCK IT OUT!
If you work in the trades or in an industrial setting, chances are you're familiar with the lockout/tagout process. It's a critical factor for protection from injury and death and some of you utilize the process on a daily basis. Others, although they should, do not perform lockout. Often, this happens in smaller job sites or smaller shops where there isn't as much concern about accidents due to a lower number of employees or less equipment and machinery. However, even in the most unlikely situations, accidents can (and do) happen. Every single day people are injured from equipment and machinery - many of which could be prevented.
Even if you own a small machine shop, it's important to protect yourself, your employes and any visitors from the potential dangers that can arise from equipment that hasn't been properly locked & tagged out. Never assume that something "will be fine like that" or that "nobody's going to touch it" and always expect the unexpected. Failure to secure equipment can result in damaged equipment, serious injury and even death - which in turn can lead to legal problems, loss of revenue and decreased productivity.
Even if you're convinced to do the right thing and begin to utilize the lockout process, where do you start? That's a good question. Depending on what type of equipment & machinery you work with there could be several answers. From locks, hasps and tags to plug and gate valve lockouts, it can be a little confusing. It might be a good idea to begin with some lockout training. This can be done as easily as researching the subject online. Additionally, you can order lockout identification & training materialssuch as books, DVD's, manuals, etc. which are especially handy for teaching employees and having a high-quality resource on hand at all times.
One of the best ways to ensure you're prepared for any lockout situation is with a lockout kit. These kits are versatile, packed with useful items necessary for performing lockout/tagout in various situations, and they're economical. The kits are also usually self-contained so they can easily be transported around the building or between job sites. If you begin to run low on certain lockout items or realize that you have a preference for certain items over others, you can always purchase more products individually to add to your kit. Some kits are even designed to cater to specific industries and are loaded with the most relevant lockout & ragout products.
LOCKOUT/TAGOUT FAILURES: PROPER PROCEDURE IS JUST THE BEGINING
When it's time to lockout and tagout, it's not only proper procedure that you should be concerned about. While following the exact protocol for a safe and 100% effective lockout is critical to your well being and the well being of others, there's more that needs to be considered.
So you've powered down some machinery, relieved a large system of piping or disabled a production line. You've followed typical protocol and begin to perform the designated service or maintenance to the equipment. But suddenly, something doesn't go as planned. You followed the lockout procedure, you took each step carefully just like you always do, yet you're finding yourself in a deadly situation and your life is flashing before your eyes. How could this be happening???
One thing that is often overlooked and has led to many accidents and injuries including fatal ones, is that although the lockout ragout procedure is performed flawlessly, the procedure is developed assuming that everything is as it should be - meaning everything is powered, connected and operational only in the manner that it's intended to be. Lockout/tagout procedures are developed specifically to prevent accidents and injury but they don't account for modification, manipulation or alteration to equipment.